While it may not be the first industry you think of when you picture Butte County, manufacturing plays a significant role in the area’s economy, creating more value per employee than other sectors including retail, government, construction or information technology.
“One employee in manufacturing is worth $616,000 to the community in Butte County, compared to one retail person with $114,000,” says Bill Gaines, chairman of Transfer Flow, Inc. and founder of the Grow Manufacturing Initiative. “If you have manufacturers in your community, your community is much more prosperous.”
One of the ways in which manufacturing can sustain the economy is by providing careers that support families through livable wages, dependable hours and good benefits.
“Even though it’s certainly not our largest sector, it is a sector that is important because of its economic contribution,” says Michael Cross, executive director of the Northern Rural Training and Employment Consortium. “There tend to be more middle class jobs, jobs with benefits, jobs that are not just part time or transitory, but someone can make a career in an industry where they wouldn’t necessarily need a college degree but can support a family and contribute to the community.”
But for many years, Butte County manufactures faced a common problem: Finding and keeping the skilled labor force needed to keep their businesses running.
“As a local workforce development board, our mission is to bring together business leaders and other community leaders to look at the labor market situation in our region, the economy and the skill needs of our region and develop programs that meet those workforce needs for the community,” says Cross. “Our thought was let’s see what common skills manufacturers need and make sure that local programs that are turning out vocational training in our area are using so our local graduates from community college programs, certificate programs or high school can walk into the workplace in our region and have relevant skills.”
Unfortunately, what they found was a lack of programs aimed at preparing students for manufacturing industry careers.
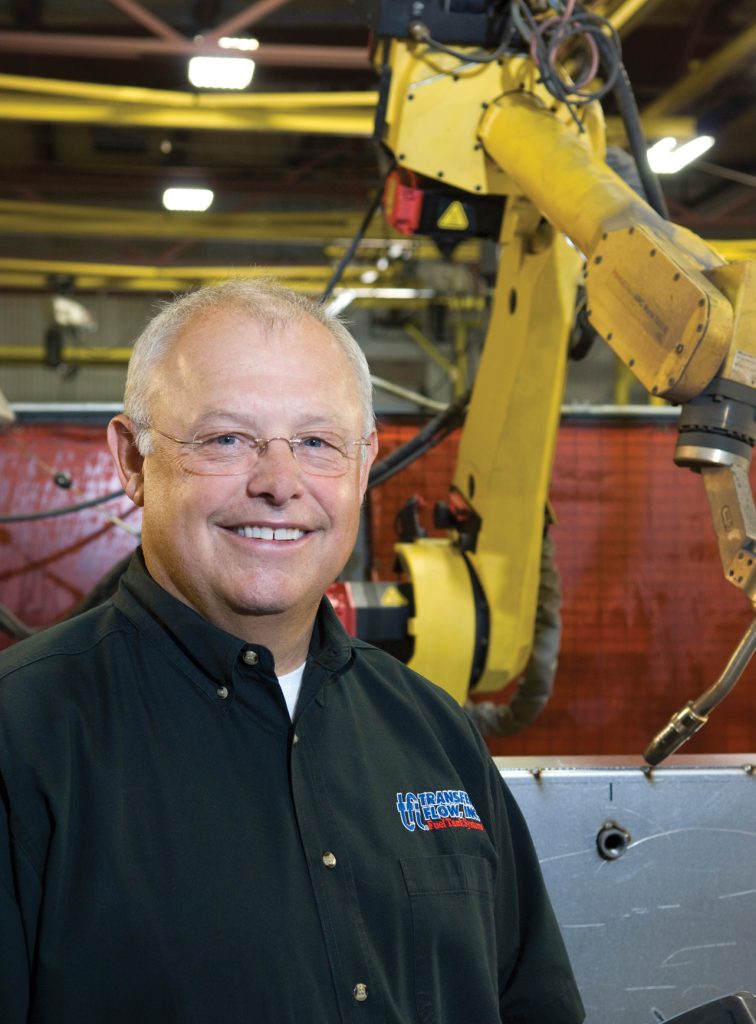
“I had the opportunity to go out and go to 26 different high schools in northern California, three community colleges and Chico State, and look at every welding, fabrication, and CAD class—if they had those classes—to find out why we could not hire a skilled labor force,” says Gaines. “What the problem was that if teachers were teaching those subjects, they were teaching what they knew, which was 20- to 40-year-old technology.”
So in 2013, NoRTEC sponsored the Grow Manufacturing Initiative, which combined the efforts of local manufacturing businesses and educational programs to develop solutions to benefit both businesses and job seekers alike.
“The point of this Grow Manufacturing Initiative was to get education involved with us so that we can work on a common issue,” Gaines explains. “This then prompted us to bring in education—the superintendents, the principals, these various north state high schools and community colleges—to tour our facilities so we could get the decision makers to understand what our problem was and then try to solve it.”
One solution was providing professional development for educators. Starting in 2014, high school teachers and community college instructors were given the opportunity to take part in short, three-day workshops that covered commonly used software, programs and best practices needed in modern manufacturing positions. After the trainings, educators could rely on the Grow Initiative organization for further support with any software or equipment issues. Within a year, several high school and community college programs starting teaching G-code, a common program used in a variety of manufacturing machinery.
Gerald Berndt, production manager, klean kanteen
“Grow Manufacturing and NoRTEC came in to help bridge that gap and to help boost collaboration between the schools and manufacturers so that they know what kids need to learn.”
“Grow Manufacturing and NoRTEC came in to help bridge that gap and to help boost collaboration between the schools and manufacturers so that they know what kids need to learn so they can come out of high school and get a good job or they can graduate and go to college and get a good part-time job with a job skill and a manufacturing trade they learned in high school,” says Gerald Berndt, production manager for Klean Kanteen. “We were looking for people who had specifically experience in manufacturing on a production line, fast-paced, quick-moving, whether it was manufacturing anything from small components to large assemblies. We definitely were needing more people who had experience in a manufacturing environment on a production line.”
Berndt, who says Klean Kanteen has been working with NoRTEC and the Grow Manufacturing Initiative for several years, says the Chico-based company has also faced difficulties finding and retaining skilled workers. He says their on-the-job training program, or OJT, was particularly helpful. Through the program, a portion of an employee’s wages are subsidized during their training period. So far, all of the trainees hired through the OTJ program have made it through their first year and are permanent employees.
“It’s really expensive to bring on new employees, so it was nice to have a portion of their wages reimbursed during that initial onboarding training period,” he says. “The OTJ training program provides a checklist that you sit down and do with the employee. … We are retaining our employees through this program. We’re getting them in quicker, trained faster, just because of this road map they have for us, and the employees are getting feedback from us based on this road map so they know where they need to improve. Because of this, they’re happier with their job.”
For more information about NoRTEC, visit www.ncen.org. To find out more about the Grow Manufacturing Initiative, including outreach programs and events for students, visit www.growmanufacturing.com.